From raw wool to finished cloth
There are many processes involved in turning raw wool into finished cloth. In the new industrial mills of the nineteenth century processes often occurred at different sites. But Salts Mill was built as a 'vertical' mill where all processes took place.
In the mid-twentieth century, Salts (Saltaire) Limited, the owners of Salts Mill at the time, produced a small booklet describing the different processes at the mill.
In our exhibition below you can scroll through the original booklet, complete with its attached samples. Then carry on to read a full set of transcripts illustrated with photographs from our wonderful Bowtell Collection.
1. Sorting
After being bought at Australian Wool Auctions, the raw wool is made into bales of 30 to 35 fleeces weighing in total about 300 lbs. each bale.
Raw wool may contain up to 50% dirt and natural grease and there are 3 or 4 differing qualities of wool on each fleece the finest is on the shoulders, where it gets more sun and is subject to least movement and wear, while the wool on the haunches receives considerable wear.
The manufacturer of differing fabrics requires wool of a particular quality, and when the bales arrive at Saltaire it is the sorters' highly skilled and important task to divide the fleeces, and grade the various parts by length and fineness of fibre.
Each quality is given a number broadly between 20 and 100, e.g. 60's (meaning 1 lb. of wool will spin a continuous thread equal to 60 hanks of yarn, 1 hank being 560 yards) 64's to spin 64 x 560 yards etc. The higher numbers denote the finest qualities and are regarded as worsteds, the lower numbers being shorter and coarser fibres as wool.
2. Scouring
Each quality in turn is passed through a "washing set" consisting of a series of tanks or "bowls" containing progressively weaker solutions of soap and alkali, then through rinsing bowls of hot water and finally through squeeze rollers.
This process removes a large part of the natural grease from the wool and also marking fluids used to identify the owners of the sheep, together with general dirt and impurities. By-products of this stage are potash and lanolin, which after refining is used pharmaceutically in the manufacture of ointments, plasters and disinfectants, and as the basis of many cosmetics. Less refined grades are widely used in the preparation of polishes, inks, vetinary preparations and soaps. Further outlets are as a base for rust preventatives, a softening agent for leather and the manufacture of special greases for high temperature lubrication.
3. Carbonising and carding
Carbonising
The prickly seeds or burrs of clover and other plants which become entangled in wool cannot be removed by scouring, and sometimes are present in too high a proportion to be dealt with by mechanical deburring machinery during the carding operation.
The wool is therefore immersed in a dilute solution of sulphuric acid and then baked at high temperature (carbonisation). The charred and brittle vegetable matter can then be removed by crushing and shaking.
Carding
The carding machine comprises a number of rollers entirely covered with pins. These succeed in removing any remaining foreign matter, at the same time dis-entangling the wool and producing a continuous sliver or untwisted ribbon of fibres.
The wool is then passed through a "Backwash" where the slivers are rewashed and dried to remove any impurities picked up during carding.
Three gilling machines are employed in turn to straighten out the fibres, preparing boxes then laying the fibres parallel within the sliver.
4. Combing
A "combed sliver" is then produced, the fibres over 3" in length being separated from the shorter fibres and other vegetable matter. These short fibres (termed noil) are of no further use to the worsted industry and are sold to the woollen industry.
The long fibres go through two more gilling operations before being wound into a ball to form a "top" made to a standard length of 255 yards and weighing about 9 lbs.
The top may be dyed at this stage for use in "yarn- dyed" or patterned fabrics, or left in its natural creamy white colour to continue through the remaining processes, being dyed after the cloth is woven to produce a "piece- dyed" or plain material.
Additional tops may be purchased from Commission Topmakers and introduced at this time.
5. Drawing
In order to make a fine, even thread the tops are blended and are then drawn out to more than 300 times their own length. This is normally done in seven or eight operations. The first three blending the material and the remainder drawing out the sliver to a fine "roving".
Highspeed modern machines with automatic and electronic controls can now complete this process in three operations, the number of personnel needed to run these machines being one third of the original requirement.
6a. Spinning
The roving is now spun into yarn of varying thicknesses and strengths as needed for different types of cloth. Each completed package of yarn can have up to ten thousand yards completely free from knots.
6b. Twisting
To give added strength, two threads can be twisted together to form a twofold yarn, or more than two threads to make a multifold yarn. Two different coloured threads may also be twisted together and used to give special effects in the design of the cloth.
7a. Winding
For ease of handling the yarn is then wound on cones or cheeses for use when making the warp or on small bobbins or "pirns" which are inserted into the shuttle and are used to supply the weft or cross thread during weaving.
7b. Warping
A number of cones or cheeses are then placed in a large open frame, the threads being wound simultaneously onto a beam in sections to form a "warp". The beam is equivalent in width to the piece of cloth to be woven, each warp varying in length from a few yards to over 1,000 yards.
8a. Weaving
After the beam has been placed in the loom, the shuttle is passed under and over the warp threads from one side to the other binding the threads together and forming the cloth.
Patterns and designs are obtained by alternately lifting different warp threads by means of healds before the weft is passed through, the weft then being beat into the cloth by means of a reed. One piece can be woven in approximately 8 16 hours dependant on the type of loom.
On the latest looms the method of taking the weft across is much faster and uses a different technique, as the weft is passed directly through the warp from the cone without the need for a shuttle. Weaving time on these looms is about one half that of automatic looms.
8b. Burling and mending
Faults caused in the weaving or earlier processes are then rectified in the Burling and Mending Department, where girls carefully examine the cloth, lifting any knots and replacing faulty threads by hand.
9a. Dyeing
The cloth is scoured to remove any dirt and impurities which it may have gathered during its previous processing.
The piece-dyed cloth is then dyed to a required shade, and rinsed. Excess water is removed from the piece by means of hydro-extraction, and the cloth dried in a hot air machine which "sets" the cloth to the required width.
9b. Finishing
The face of the cloth is then cleaned of any excess fibre by the cropping (Cutting) machine.
If required the cloth can be London Shrunk to prevent later shrinking; in this process the cloth is folded into blankets which are soaked in water, and allowed to stand over-night. The cloth is then hung up to dry for a day. After it is taken down, it is relaxed and has its own natural water content.
9c. Packing and dispatch
The cloth is then pressed and is ready to be sent to the Warehouse where all pieces are finally examined for any faults, measured, weighed, and packed for despatch to the customer.
You may also be interested in
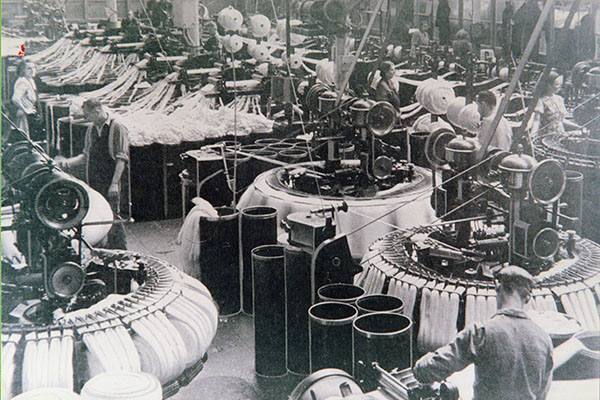
Find more items in our collection concerned with the textile industry and the world of work in Saltaire
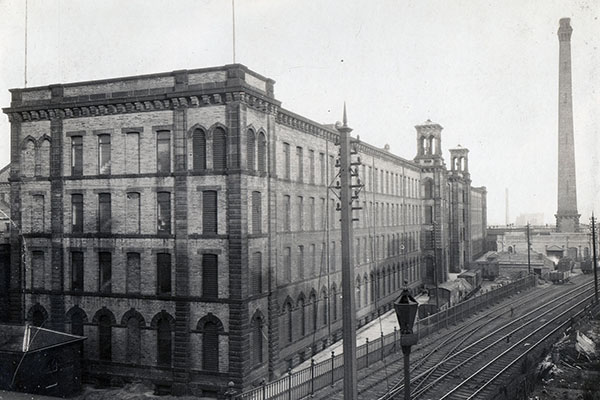
Discover more about Salts Mill using our Mill and Owners timelines, workers personal memories, and the post-textiles story of Pace Micro Technology
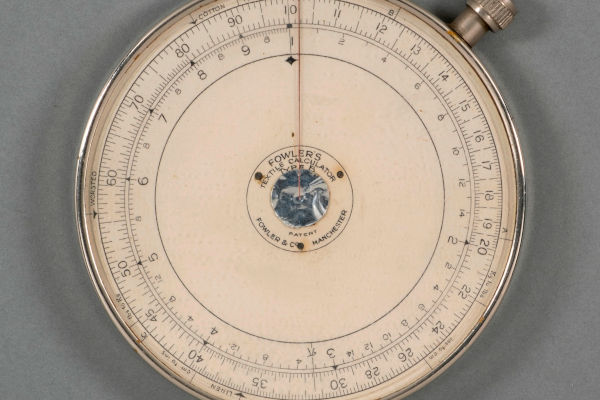
Browse the collection donated by Albert Bowtell containing photographs, documents and items related to Salts Mill